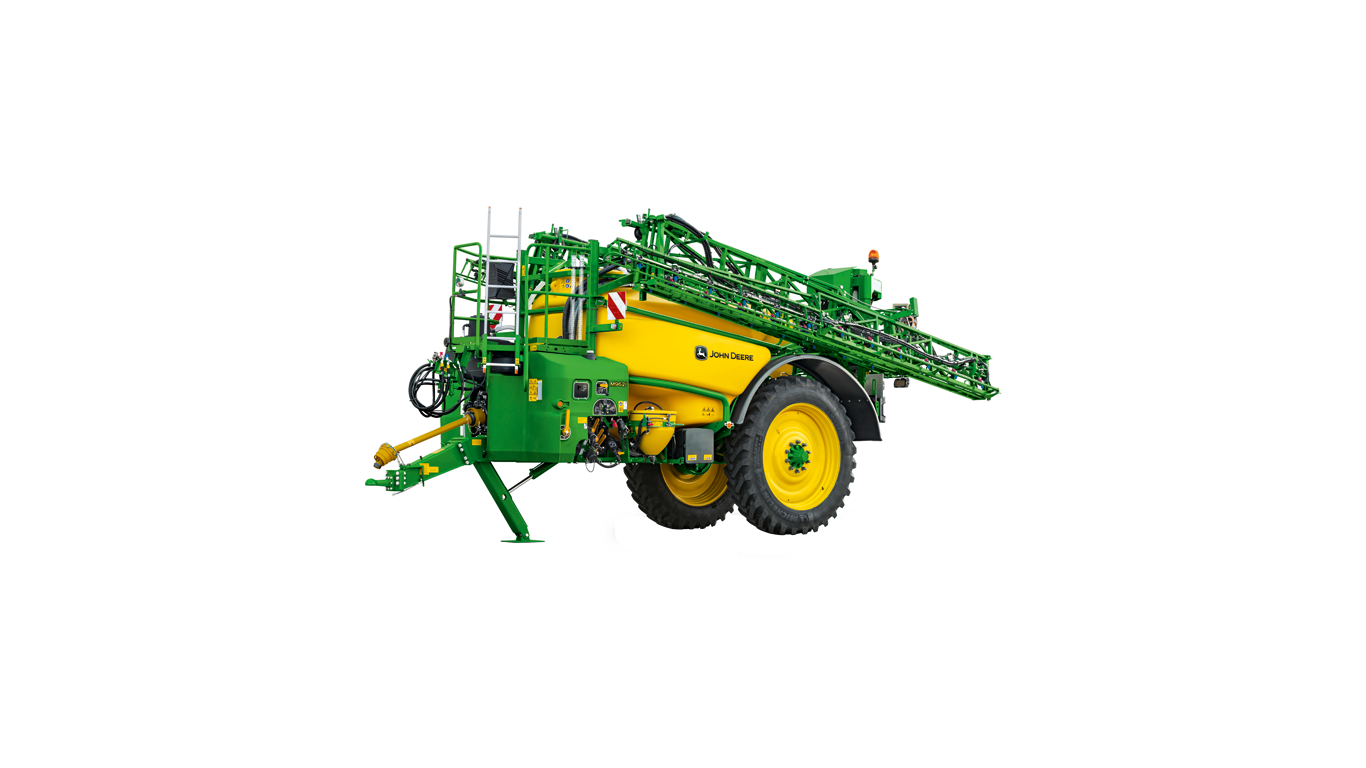
M962i
Trailed Sprayer
- 6,200 L tank volume
- 620 L rinse tank
- 2 x 280 L/min pump capacity (max 250 L/min to boom)
- Optional BoomTrac™ automatic boom tilt and height control with headland management
Specifications
Click below for more info
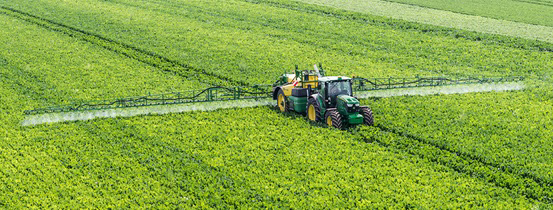
When it comes to uptime, the M900 Series is designed based on the same insights as the John Deere R900i platform, using similar proven components such as tank, boom, frame, and axles to meet quality and reliability levels that are expected from a high-quality trailed sprayer.
The round-shaped polyethylene tank is fully cradled by the frame and gives the machine a low center of gravity. Together with the standard double-linked ProRoad axle suspension, stability on the road and in the field are built-in.
When it comes to capacity, there are three tank sizes available: 4400 L (1163 gal.) on the M944, 5200 L (1374 gal.) on the M952, or 6200 L (1638 gal.) on the M962. With a selection of full-range durable steel spray booms from 24 m up to 40 m (79 to 131 ft)* and different spray systems and automation levels, producers ca customize the configuration to their needs.
*NOTE: Check the price list for possible configuration combinations.
Features of the M944, M952, and M962 Sprayers:
- Standard three-pole, 12-V COBO connector
- Ease of use: manual or semi-automatic operator’s station
- Comfort: full electrohydraulic control with or without load sense
- Ringline or pressure recirculation spray system layout with 50-cm (20-in.) nozzle spacing up to nine sections
- Ease of use: multi-function lever for sprayer operation and choice of Implement Display 1100, G5 Universal, or G5Plus Universal Display
Features of the M944i, M952i, and M962i Sprayers:
- ISOBUS ready communication
- Ease of use: manual or semi-automatic functionality operator’s station
- Ringline, pressure recirculation, or TwinSelect™ individual nozzle control spray systems with 50-cm (20-in.) spacing
- Pressure recirculation spray system with 25-cm (10-in.) nozzle spacing up to 15 (virtual) sections
- Comfort: full electrohydraulic control with or without load sense and with or without multi-function lever for sprayer operation
- Choice of displays: G5 Universal, G5Plus Universal Display, or less display to connect to John Deere ISOBUS tractors with an in-cab CommandCenter™ display
- Section Control ready
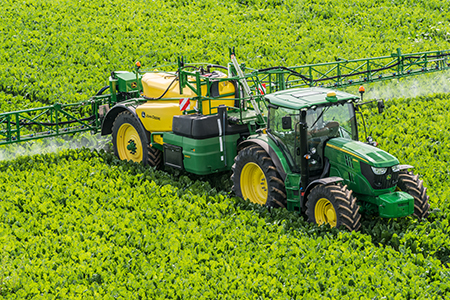
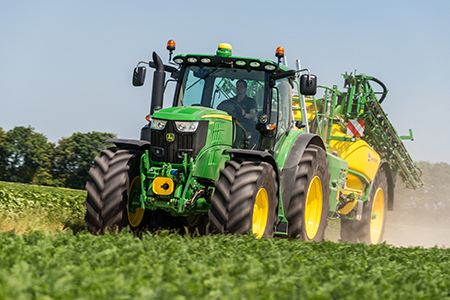
The round-shaped polyethylene tank is fully cradled by the frame and gives the machine a low center of gravity. This comes together with the standard double-linked ProRoad axle suspension, providing stability on the road or in the field.
With its low center of gravity and even weight distribution, the M900 Series is built for stability. The entire mainframe is designed especially for the job. The heart of the mainframe is the cross structure in the center section to redirect forces, providing strength for a long lifetime. The frame design cradles the large polyethylene tank perfectly. The special tank shape offers deep sump while the steeply sloping bottom limits chemical residues. Due to the special tank design, additional tank baffles are not needed. It is easier to agitate liquid due to the smooth tank that has less risk of spray solution sticking to the inside of the tank.
The heavy-duty axle is fully integrated and comes standard with ProRoad double-linked axle suspension.
The frame, tank, and single axle design offer better maneuverability. Regardless of the boom position, the level weight distribution helps to always keep the machine steady.
Benefits of tank frame axle design include:
- Frame axle and tank design with lower center point of gravity supports stability in the field and on the road
- Round-shape polyethylene tank with smooth surface for perfect agitation and easier rinsing inside and outside
- Deep sump for better emptying, even on hillsides
- No baffles or dead corners supports better solution mixing
- Perfect readout with dual stage dry liquid level indicator that comes standard (digital tank level indication is optional)
- ProRoad double-linked fixed or steering axle offers better maneuverability and prevents leaning in corners
- Axle suspension with four maintenance-free polyurethane dampers absorb the shocks, providing stability and uptime
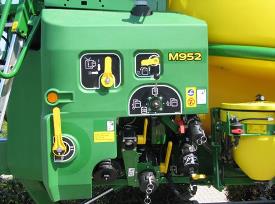
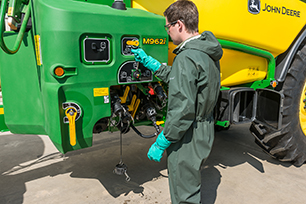
The ergonomic design of the operator’s station makes operation easy and convenient. The large handles make valves easy to set, and synchro positioning helps limit mistakes and makes filling, spraying, and rinsing easier.
The standard non-return check valve in the system prevents back flow through the filling hose. This prevents point-source pollution and chemical spillage and protects the environment.
The PowrFill chemical inductor hopper, spray gun, and clothing lockers are partly stored behind the valve area. Filters and hose connections are protected and easily accessible for operation, cleaning, or maintenance.
The chemical safety card holder is located near the platform, making the information readily available.
Benefits of operator’s station design include:
- Less risk of mistakes with easy-to-set manual valves with large handles
- Faster filling with 7.62-cm (3-in.) fill hose connection with non-return system check valve in base
- 08-cm (2-in.) transfer valve to transfer liquid from main tank to external point
- 08-cm (2-in.) quick connector for filling rinse water tank (optional)
- Safe filling with closed chemical transfer connection (optional)
- PowrFill chemical eductor hopper (optional)
- Clothing locker with two compartments (optional)
- Built-in primary pressure regulator ensures a constant 10-bar (145-psi) pressure for eductor, agitation, and manually controlled rinsing nozzle regardless of the spray pressure setting
- Manual on-off agitation is based on injectors, with optional automatic on-off switch to reduce risk of foaming
- Recirculation valve enables efficient usage of 600-L (158-gal.) rinse water tank content
- 18-L (4.75-gal.) hand-wash tank with refill position tap at operator’s station
- Easy to access both solution system filters
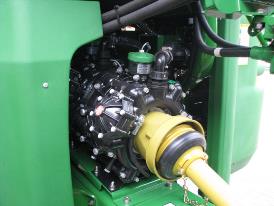
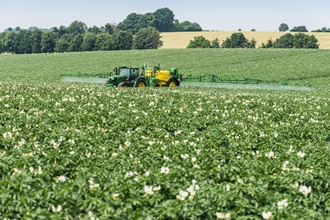
The M900 and M900i models are equipped with two durable, 6-cylinder self-priming piston diaphragm pumps designed for spray tasks.
Pumps and filling connections are in protective positions on top of the frame and partly protected by the covers. Connect the 7.62-cm (3-in.) filling hose to 7.62-cm (3-in.) filling connection; select the levers and filling starts.
An integrated, non-return check valve prevents a system backflow. The ball valve at the filling hose connection comes standard to allow easier disconnection of the filling hose.
- Two self-priming pumps with 560-L (148-gal.) capacity and a collective 12 cylinders work together when filling
- In spray mode, one pump is used for spraying and one pump is used for agitation functions
- Solution system flow delivers a maximum output to the boom of 250 L/min (66 gpm)
- Pumps are located on top of the mainframe to keep clearance at the drawbar and remain protected by shielding
- Camlock coupling with blind cap and 7.62-cm (3-in.) filling connection
- Maximum pump technical pressure is 20 bar (290 psi), and the system axillary pressure is set to 10 bar (145 psi) to support a longer pump lifetime
- Non-return check valve in the solution system prevents backflow
- Optional pump oil level sensors display warning when pump oil level is insufficient
- Pump drive – wide-angle power take-off (PTO) is in base, hydraulic motor for pump drive is optional
- Pump protection – using the filling connection, liquid entering the pump passes a large 30-mesh filter first
Once low flow application rates are frequently used, it is highly recommended to upgrade the machine with the low flow rate bypass kit (BWZ10081).